We've built robust rail flaw detection software tools to ensure superb data analysis.
Dual Display Formats
Nordco's Windows-based rail flaw inspection software processes ultrasonic data to measure signal amplitude, signal time, and distance traveled.
Operator-controlled functionality includes channel gates, gains, and thresholds. Two independent display formats are available:
-
Strip Chart Event Recorder format - quickly shows potential defects using channel patterns. Typical data responses appear on the three main channels; any indications on other channels potentially mean a possible defect. Operators monitor the channels on the strip charts, watching for indications outside the main channels. When a flaw indication appears, operators re-test the rail segment to confirm that the indication is repeatable and consistent. If yes, the operator marks the rail segment for further analysis.
-
Consolidated B-Scan format - quickly shows a cross-sectional plane view of a rail segment, displayed as a two-dimensional plot. Similar to the strip chart format, typical data responses appear in the main channels area; any indications outside that area potentially mean a possible defect. Operators monitor the channels on the B-scan, watching for abnormal indications. When a flaw indication appears, operators re-test the rail segment to confirm that the indication is repeatable and consistent. If yes, the operator marks the rail segment for further analysis.
On-Board Run-on-Run software
Run-on-Run is a comparative analytical tool that compares prior test results to current test results for the same portion of the rail.
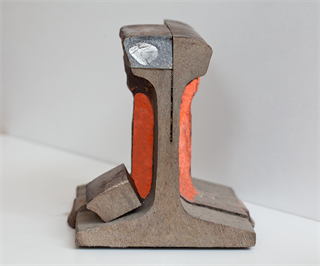
The system alerts the operator of a match to a prior indication and allows for real-time comparison and the opportunity to identify any changes in the rail's health.
The system uses the GPS location as well as the track structure itself to identify where the vehicle is currently testing. The system is then able to retrieve historical data from previous test runs, including the previous icons used, rail side, defect location, and defect size, and display that data to the operator.
When the system determines that a current defect indication matches an indication from a previous test, the operator is alerted. The operator is then able to use the historical data to make informed testing decisions.
Pattern Defect Recognition engine
Our engine incorporates multi-level artificial intelligence to recognize common rail conditions, as well as recognize and classify defects.
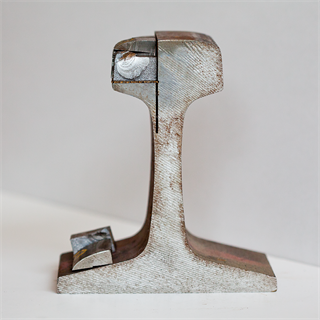
This is an adaptive learning system that adds new defects to the library as they are analyzed, allowing the system to recognize new defects automatically.
On one level, the system recognizes that it has encountered a certain rail structure, such as a joint. Therefore, when there are indications outside that rail structure, the system classifies these outside indications as defects. On another level, the system looks inside the rail structure, i.e. a joint, to determine if any anomalies appear outside the normal parameters of that rail structure. if yes, the anomalies are displayed separately on the right side of the screen, alerting the operator to analyze it more closely.
This multi-level assessment reduces the number of operator errors attributed to fatigue and stress, since it reduces the number of defects that the operator needs to asses. In addition, the adaptive learning capability means that as more defects are assessed, the library of recognizable defects grows for future use.